扶桑精工ができること
節電のノウハウ

毎年の使用量ダウン
弊社には節電のノウハウがあります。
節電コンサルタントに頼めば高額な費用がかかりますが、別に難しいことではありません。自分たちの手でできることがほとんどです。
ひとつチャレンジしてみられてはいかがでしょうか。もちろん、費用をいただいて作業というのも大歓迎です。現状、特に何もしていない状態で、夏場に冷房を使用していれば、電気代の25%を削減することが可能です。
弊社の場合、年間1000万以上の料金削減となりました。
下のグラフは弊社の2010年からの使用電力の記録です。年々使用量が下がっているのがわかるでしょうか。何が効き目があったのかを、以下にお話しします。
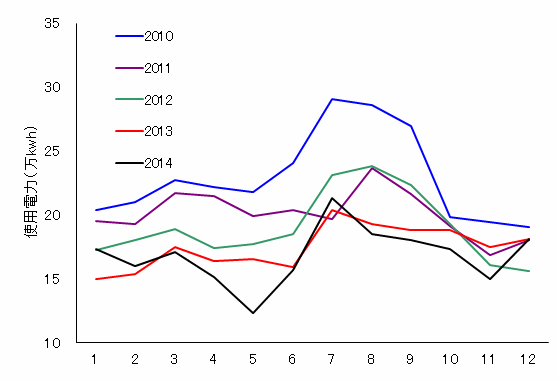
最初に
2010年は暑い年でした。
6月終わりに試運転をしたのを皮切りに、冷房が始まりました。9月まで、電力使用量はもちろん、デマンド値(30分当たりの使用量)も過去最高になりました。
デマンド値の説明
使用電力が50kwを超えるあたりから、一般家庭で採用している低圧受電契約よりも高圧受電契約の方が、割安になってきます。工場などはほとんどが高圧受電契約です。
高圧受電契約は毎月一定の基本料金と、使った電力に応じて課金される従量料金の合計で支払います。基本料金は低圧受電契約より高いですが、従量料金は安めに設定されています。
これはある程度大口の使用者は、安く電気を利用できる代わりに、発電・送電設備の設備費を基本料金によって、多目に負担するという考えです。
高圧受電契約の基本料金は年間を通して、30分間の電力の最大値に応じた金額で定められます。弊社では、もっとも電力を使用するのは冷房費用ですから、真夏の1日にグーンと上がった電力メーターによって1年間、高い基本料を払い続けることになります。
電力会社は最大の使用量に応じて、設備を増設する必要がありますから、納得できる方式でもあります。
高圧受電契約の場合、全体の使用量を下げることも重要ですが、このデマンド値を下げることが、最大の狙いになってきます。
見える化
改善を志す時、最初にすべきことは見える化です。
弊社は2011年にデマンド監視装置を設置しました。電気が、いつ、どこで、どのように使われているかを知るためです。
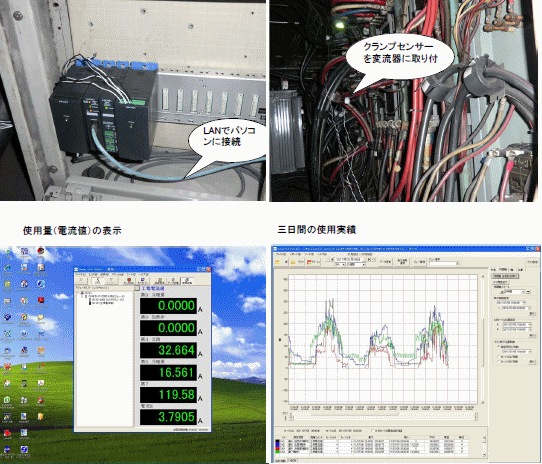
社内の電気主任技術者が設置しましたので、装置費用だけで済み、およそ40万でした。
その結果によると
・夏場のデマンドの半分以上が冷房であること
・冷やし始めと、電動機のスイッチが一斉に入る時間帯に最大になること
などがわかりました。
機械はストップできませんが、冷房はある程度、使用量を減らすことができます。連続して運転していれば、途中で間引き運転しても、「少し効きが悪いかな?」程度で済むものです。
2011年は東北で大地震があり、世間的に節電気運が高まっていました。弊社は関西にありますので、直接に影響はありませんでしたが、神戸の地震のことも思い出しつつ、「関東でがんばっているのだから、関西でもできるだけ協力しよう!」と全員で心を一つにしました。
元々の契約によるデマンド値は900kwでしたが、15%削減の765kwを目標にしました。
関西で節電しても、周波数の違いであまり関東には送れないと、後で知りましたが、翌年以降に我が身を助けることになります。
温度がターゲットですから、社内の各所に温度計を設置しました。弊社の工場はすべて社内LANで結ばれています。各所のPCにUSBに挿すタイプの温度計を設置しました。15か所に設置して2万円くらいです。測定したデータは社内のソフト開発部隊が集中して監視できるソフトを作りました。
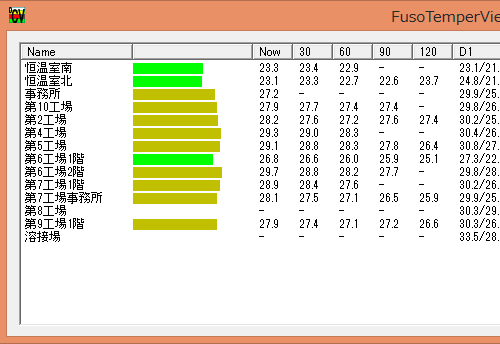
ここから先が大事なところです。
使用量を実際に減らさないと、意味がありません。
運転開始を遅らせる(30℃を越えるまでは、運転を始めない)
これは冷房機の運転単位ごとに実施しました。そのための15か所の測定点です。夏は朝方でも25℃以上ありますから、25~30℃の管理になって、機械の精度的にも特に問題はありません。
恒温室や溶接場など、特別なところは特別な対応としました。
実際に運用すると、案外冷えすぎているところが多いことに気付きます。この機会に運転台数を減らして、扇風機で平均化することにします。
これだけでも使用量が減りますし、機械精度にプラスになります。
使用量が多い時は間引きする
デマンド監視装置が、目標値を越えそうと警報を出すと、運転パターンを変え、1時間運転しては、30分止めるというように、手動でスイッチを切りました(自動で切る装置は2011年には、まだ設置していませんでした)。
真夏になると警報も頻繁になり、操作は結構大変でした。それでも無事に目標を達成でき、秋になるとほっとしたものです。
翌年は自動でON、OFFできる装置を設置し、ずっと楽に節電できるようになりました。こちらも社内で開発した装置でしたので、40万くらいで設置ができました。
2012年は原発が再運転できず、関西でも節電目標が設定されました。世間的にはかなり厳しい話でしたが、弊社の場合は既にクリアできていたので、あまり無理しすぎないよう、デマンド値の範囲内で、むしろ2011年より涼しく過ごせたように思います。
風を味方に
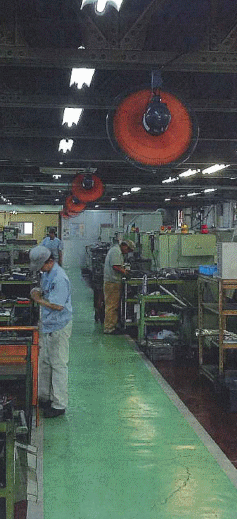
冷房を規制するため、できるだけ外気を導入して、工場内の温度を上げないようにしました。
局所的に扇風機をあてても、モーターの発熱などで、部屋全体ではかえって上がってしまうものです。
弊社の場合、立地条件から西の風が多く、その風を東に抜くよう、連続して扇風機を設置しました。
外気温が上がり過ぎる真夏は扇風機だけでは過ごせませんが、真夏以外では結構効果があります。
作業レイアウトの変更
弊社には溶接部門があり、加熱炉で予熱して、溶接を行っています。手元に真っ赤に焼けた鉄(600℃!)を抱えるような格好で作業を行うハードな作業です。
過去からのしがらみがあり、複数個所で作業していましたが、この機会にまとめてしまい。加熱した部屋を冷やすような無駄をなくしました。
溶接部門がなくなった棟は、冷房に要する電力が格段にさがりました。
溶接部門には、徹底的に換気できるようにすると共に、スポットクーラーを配置して対策しました。
遮熱
3種類を実施しました。
ゴーヤ
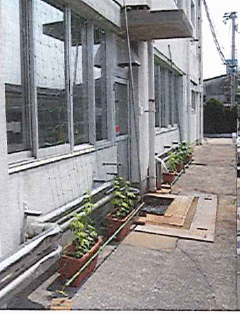
植物を育てることは楽しくもあり、緑を見ると癒されますが、会社の場合、休日の水やりなどの世話が難しいです。特に盆休みなど、最悪な感じになってしまいます。
遮熱フィルム
値段の割に効果があります。まったく同一条件で貼っているところと、貼っていないところの比較ができないので、数字データはありませんが、体感でかなり感じます。
事務所・工場の施工できるところは全て施工しました。
フィルムを貼ることによって、ガラスにひびが入ることがあります。
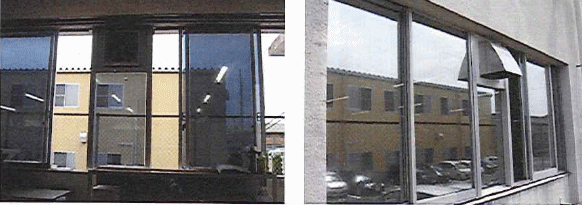
遮熱塗料
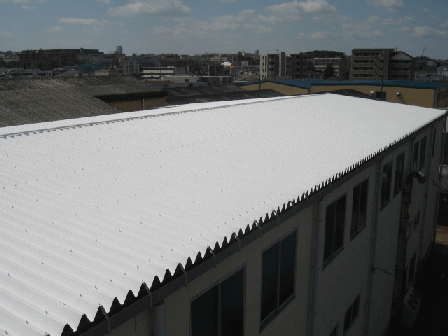
工場の折板屋根に施工しました。
かなり効果があります。屋根裏がある棟に施工したのですが、室温で1.5℃下がりました。エアコンの効きが良くなったのと、夕方になって天井から頭を炙られる感じがなくなりました。
効果はありましたが、これからは遮熱塗料よりも、太陽光発電かもしれません。設置すれば遮熱にもなりますし。
見える化2
弊社の工場エアは複数台のコンプレッサーをプログラム運転して、使用エア量の変化に対応する方式です。
大きなインバーター式のコンプレッサー1台で調整する方式もありますが、故障の際に工場ストップになってしまうのと、やはり定格で運転するのが一番効率が良いだろうという考えです。
2011年には4台の定格運転機と、1台のインバーター機を組み合わせて運転していました。昼間の使用量が多い時には3台の定格機と、1台のインバーター機を運転し、夜間の少ない時には1台の定格機と、1台のインバーター機だけを運転します。1台は予備になります。
保有機の1台が古くなってきたので、更新するのを機会に、すべての機械に流量計を設置して、エア吐出性能を測定してみました。
測定中、ショッキングなことが判明しました。
なんと、よく運転している1台は、吐出量がほとんどありませんでした。
2011年から2012年の使用電力の節減の半分はこの「無駄飯喰らい」の改善でした。
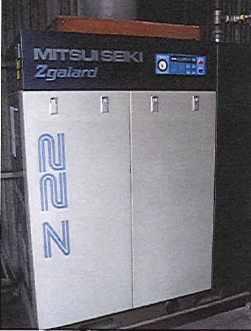
インバータ化
油圧装置のインバータ化もかなり効果があります。
複数台の合計ですが、月々の使用量を1万kwh以上、引き下げる効果がありました。
施工前はインバータ化での追従性がやや心配でしたが、まったく問題ありませんでした。
思わぬ効果もありました。インバータ化によって油温が下がり、機械の動作が今までより安定したのです。
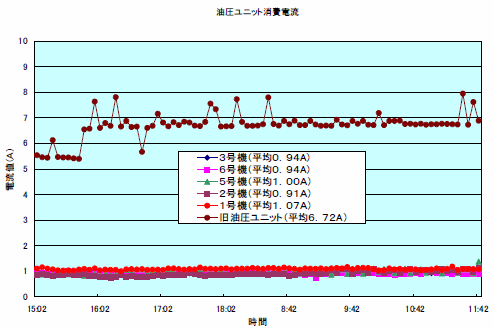
照明改善
工場棟の高天井は全てLEDに変更しました。元が400Wの水銀灯でしたが、光束を絞って100WのLEDとしました。同じ明るさ範囲の時は160Wくらい必要らしいですが、弊社の場合、100Wの範囲で十分でした。
事務所棟の天井は反射式の蛍光灯に変更しました。
事務所棟をLEDにしないのか?と疑問を持たれる方もいるでしょう。導入時点では十分に明るくて、安いLED照明がなかったのです。最近になって某パナソニックから かなり良いものが出てきました。
2012年から2013年の使用電力の節減の半分は照明の効果です。
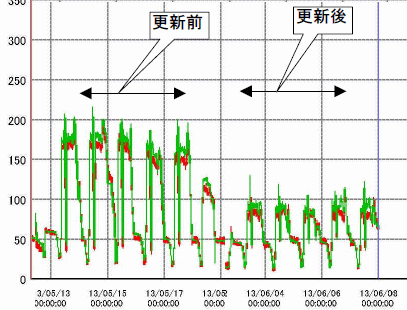
電力の単価で条件は異なります。弊社の場合、以下のようになります。
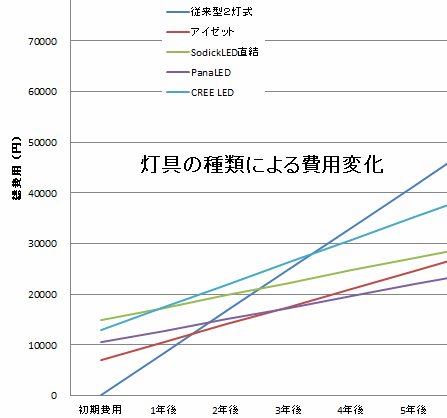
トランスの変更

弊社の工場は数十年を経過し、変電設備も定期的に更新はしていますが、全体に古くなっていました。
この機会にスーパーアモルファスに置き換えました。
変更前は「ほんと?」という感じでしたが、今は「ホント!」です。
確かに効果あります。置き換え計画があるなら、多少高くても、ぜひ、こちらにしてみてください。
2012年から2013年の使用電力の節減の半分はトランスの効果です。
2013総括
最終的には、電気代の値上がりもあり、2010年レベルの電気代となっています(むしろ高いかも…)。
トホホです。
しかしながら、これらの活動がなければ、25%以上アップの電気代となっていたかと思うと、これもまた恐ろしい感じですね。
空調を電化
電気代はどんどん値上がりするため、節電も進歩していく必要があります。
2014年には、一部冷房を空冷化しました。
これまでは集中式の灯油燃焼熱吸収式を使用していました。一見、節電に逆行するように思えますが、設備してから25年を経過していますので、機器自体の効率もかなり落ち、電力をかなり使用する割に、効きがよくありませんでした。
7月こそ前年を若干オーバーしましたが、それ以降は適切に使用しても少ない使用量となりました。
もちろん、夏場にボイラーで燃焼させていた灯油代は0円になっています。
定期的な設備の見直しが大事
準恒温室化
精度を安定させるには温度が安定している必要があります。
最近の機械ではサーモフレンドリーなど、いろいろな仕組みでサポートをするようになっていますが、室温が一定していれば、さらに安定することでしょう。
弊社では最も精度を必要とする品物は恒温室で加工を行います。しかしながら、すべての作業場を恒温化するのは費用がかかりますし、何より維持費が大変です。そこで、準恒温室化して、空調費を抑えながら温度変化を少なくするようにしました。
と言っても特にむずかしいことをしたわけではありません。
隙間をふさぐ
工場ですので、搬入用の大扉があって、こちらには結構な隙間があいています。
徹底的に塞いでしまいます。
扉は鉄でできていますので、断熱塗料を塗り、一部はウレタンスポンジを貼りました。
窓を2重化する
窓は結構熱が出入りします。
サッシの隙間から空気が流通しますし、窓ガラスから入る太陽光線は強力な熱量です。
窓枠は通常金属ですので、そちらの伝導熱もバカになりません。
冬場に測定しますと、暖房の入った工場でも、窓ガラスが一番温度が低くなっています。
断熱塗料でガラスを塗ってしまうと若干効果ありますが、それよりもプラ段のようなもので、窓全体を覆ってしまうのがもっとも効果あります。
下記は、準恒温室化した工場の温度変化です。
2013年に比べると、2014年が良くコントロールされているのがわかると思います。
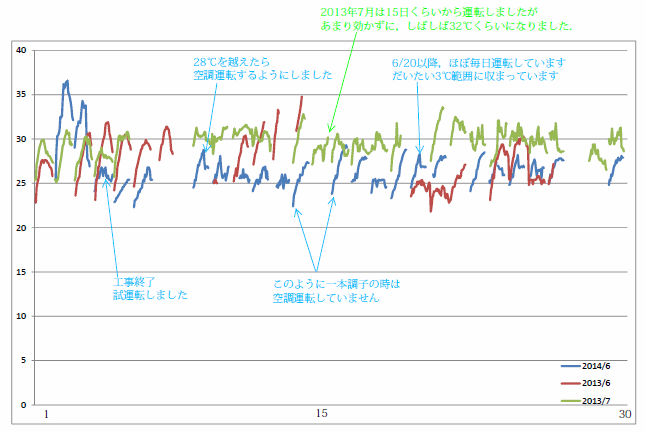
これでも2013年とほとんど同じ電気使用量ですから、採用しない手はないでしょう。
太陽光発電
工場の全ての屋根に発電パネルを設置しました。
全量を売電しますので、節電としては出ませんが、工場の温度も下がったような気がします。
詳しくは電力事業部のページでご覧ください。
勾配の緩い折板屋根は全面に、勾配のきついスレートの屋根は南側に太陽電池パネルを貼っています。
勾配の緩い折板屋根は全面に、勾配のきついスレートの屋根は南側に太陽電池パネルを貼っています。

全景ではこのようになります。
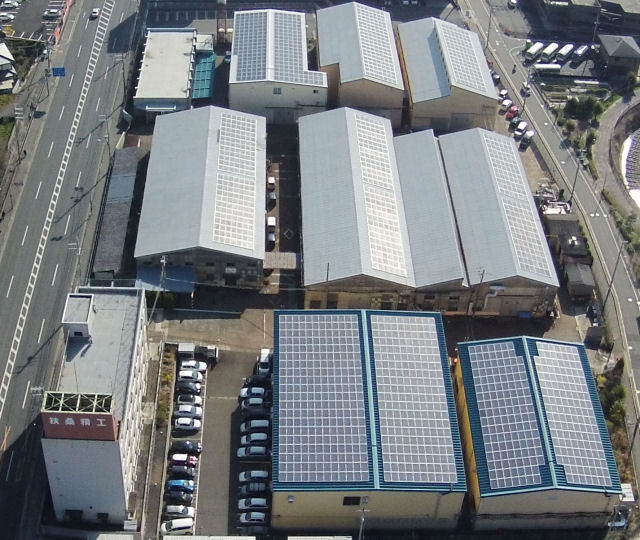